Case Study
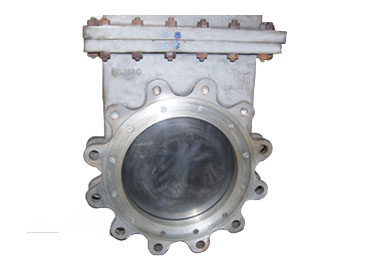
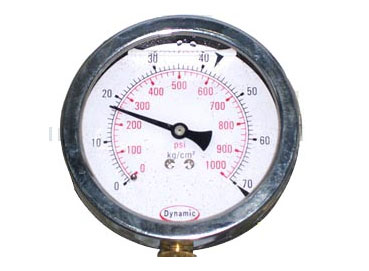
Almost every known fluid in industry through the world can be, and is , handled by the diaphragm valves.
This is in the year 2008 when we got an enquiry from our buyer M/s ESSAR OIL REFINERY for their requirements of FGD Valves for their refinery unit in Jamnagar.
The valves required were of very critical nature and required considerable engineering from our side. The entire job was supervised by EIL (Engineers India Ltd – A pioneer institution in Petrochemical Sector in India and world) along with ABB LUMMUS CREST of Mauritius . Inspection was to be carried out by ESSAR / BUREAU VERITAS As such the technical requirements were very exhaustive. They wanted a pressure class of 300# for their requirements in 600MM size and that too with motorised actiator which is not manufactured in India.
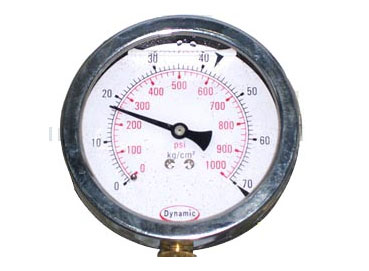
We at UNIMAC decided to have a go with the technical parameters and Bid for this tender from ESSAR. Technical wing from ESSAR had a detailed discussion with us regarding fulfillment of all technical parameters as laid down by EIL & ABB. We knew it was very difficult but not impossible so we confirmed all the technical requirements of ESSAR and won the order.
The real challenge started after getting the order. The prices of raw materials started to shoot up at that time. We were lucky enough to have the castings received on time by our casting vendor who also had worked very hard with us to meet the deadline. Our other vendors also chipped in with other spares required for valves and finally we got the smaller sizes valves assembled first for inspection. The inspection went smoothly with one or two hiccups but ultimately we managed to deliver first lot of valves of smaller sizes of 6” and 12 “with in stipulated time.
After that we started process of assembling of 600mm valves as all the components have arrived by then and we tested the valve at our works. To our utmost surpise the valves bonnet began to bulge when we applied the pressure of more than 150 psi. This was the real test of us. We cheekd with various experts also and they all have confirmed that pressure class of 300# is not possible on 600mm size and they have informed us that we will not succeed. ESSAR was pressurizing us for valves and we have explained to them the difficulties faced by us. We have assured them we will work out some ways to succeed in this project and they supported us with patience.
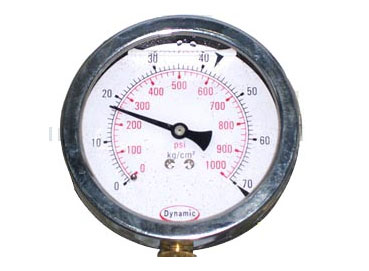
We rechecked our engineering and redesigned the valves’ bonnet once again. This time we have taken suggestions from various persons starting from foundry man to pattern making , designing, machining etc and redesigned our bonnets for valves and took sample castings for assembly. To our utter surprise, the valves withstood the required pressure. We immediately informed ESSAR of the good news and went ahead with remaining castings of valves. The castings were perfect and after assembly it all passed out with flying colors
The actuators were supplied by ROTORK with the technical parameters as laid down by the EIL. The actuators were installed under their supervision. We must thank ROTORK also for providing us the services of their engineers as and when we required them.
For this job we want to thank ESSAR for their patience and co-operation extended to us during our difficult times. Also our sub vendors who have worked with us day and night for this job and stood by us. Without their support it would not have been possible. And last but not the least the Inspectors from ESSAR & Bureau Veritas for their co-operation extended during inspection of valves at our works.
We at UNIMAC are now confident of doing challenging jobs. We are sure that one must believe in his/her abilities and have faith in Almighty God.